Introduction
The fantastic world of injection molding unfolds with myriad possibilities. From the tiny Lego bricks to our everyday use plastic utensils, to critical components in the automotive and aerospace industry, injection molding technology is everywhere. But to navigate among its complex pathways, it is essential first to grasp various aspects—and this is where we begin our journey today.
Material Selection for Injection Molding
The material forms the soul of the molded part and plays a critical role in determining performance characteristics, cost-effectiveness, and environmental footprint. Thermoplastics, thermosets, silicones, metals, even glass—the list of usable materials is ever-growing. However, each material brings its unique properties to the table, affecting moldability, strength, temperature and chemical resistance, and much more. Plastic materials like polystyrene, polyethylene, and ABS (acrylonitrile butadiene styrene) are popular choices due to their robust physical properties and cost-effectiveness.
The Importance of Mold Design in Injection Molding
Mold design is the lifeblood of a successful injection molding process. Wall thickness, draft angles, gate locations, cooling line placements, and ejection system design – these all form part of a complex balance that can make or break your molding process. However, with advanced CAD/CAM software and experienced engineers’ insights, an efficient, cost-effective, and truly optimized mold design can be achieved.
Differences between Single Cavity and Multi-Cavity Molds
A single cavity mold is designed to create one unit per cycle, ensuring consistency in every product. Multi-cavity molds, with their capacity to shape multiple identical parts simultaneously during a cycle, offer substantially higher production speeds. However, the key to perfect replication across every cavity lies in precise balance and uniformity which can be a challenging task to achieve.
Understanding Injection Molding Materials
Materials used in injection molding are generally thermoplastic polymers—granules that melt when heated, take the mold’s shape when injected, and finally solidify to form the part. Each material comes with its set of properties; for instance, polystyrene is low-cost and easy to mold but brittle, while polyethylene is cheap, durable, and resistant to many chemicals.
Common Types of Plastics Used in Injection Molding
A variety of plastics find their applications in the injection molding industry, each with unique properties and uses. Polyethylene (PE), known for its high impact resistance, is often used for manufacturing products such as durable toys, milk jugs, and disposable cutlery. Polypropylene (PP), with its high resistance to chemicals, is typically used to create rigid packaging, laboratory equipment, and medical appliances.
Furthermore, Acrylonitrile Butadiene Styrene (ABS) holds a strong presence in injection molding. Renowned for its resistance to physical impacts and toughness, ABS is frequently used for making protective housings, such as those around power tools and electronic equipment parts or toys like LEGO bricks.
Polycarbonate (PC) is a robust and transparent engineering plastic with high strength, toughness, and optical clarity. It is commonly used to make products requiring transparency and impact resistance, such as eyewear, automotive components like car bumpers and windows, and even CDs and DVDs.
Thermoplastic Elastomers (TPE) amalgamate the elasticity of rubber with the processability of plastics. They are often molded into goods requiring flexibility and durability, such as wire insulation, flexible automotive parts, shoe soles, and soft grips on tools.
Understanding the characteristics of these common types of plastic can provide a basis for selecting appropriate materials for your injection molding project.
Equipment and Tools Used in Injection Molding
A typical injection molding setup consists of an injection machine, a mold, and raw plastic material. The injection machine is tasked with melting the plastic granules and injecting them into the mold, which cools and solidifies into the desired shape.
Factors Affecting Injection Molding Quality
Quality control in injection molding depends on several factors—mold design, clamping force, injection velocity, and cooling time being among the most crucial ones. To guarantee consistently high quality, these variables need careful monitoring and control.
Common Defects and Solutions in Injection Molding
Common defects such as warping, sink marks, bubbles, and flash can occur, often due to irregular cooling, imprecise pressures, or imperfect mold design. Developing an understanding of these defects, along with their remedies—often tweaks in process parameters or mold design—can be invaluable for high-quality output.
Case Study: Producing Plastic Lego Bricks
Lego, a name synonymous with creative play, is a fantastic example of precision injection molding. These iconic plastic bricks that have been engaging minds young and old for decades are the result of high-grade and very precise injection molding.
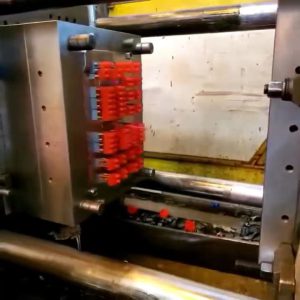
Material SelectionThe Lego Group has a commitment to quality and durability, using a high-grade plastic polymer, acrylonitrile-butadiene-styrene (ABS), for their bricks. ABS was chosen for its excellent balance of strength, flexibility, and color stability. These qualities contribute to a Lego brick’s ability to be used repeatedly without significant wear or color fade.
The Molding ProcessThe process begins with the ABS granules being heated to a temperature of 232°C, turning the material into a malleable state. The heated ABS is then injected into the highly precise moulds at a pressure of up to 150 tons, which shapes the bricks.Every Lego mold is precision-machined to a fraction of a millimeter to ensure that the bricks it produces will fit together with others perfectly. This level of exactness results in the signature ‘clutch power’ – the snapping fit between Lego bricks that holds them together.
Cooling and EjectionAfter the injection, the ABS is allowed to cool and solidify inside the mold. The cooling process is carefully controlled to reduce warping or shrinkage of the bricks. Once cooled, the Lego bricks are ejected from the mold, inspected for quality, and sent off to be played with by Lego lovers worldwide.
Sustainability CommitmentIn addition to the technical side of molding Lego bricks, it’s also worth mentioning that the Lego Group is committed to sustainability. They aim to use sustainable materials in all core products and packaging and achieve zero waste in operations by 2030. Their search for a more sustainable material that matches ABS’s versatility and durability is ongoing.
Looking at the production of Lego bricks, you can see the complexities and precision needed in injection molding. It’s a testament to how much thought, design, and engineering go into what might seem like simple plastic bricks at first glance. The commitment to providing a high-quality product that can outlast even the toughest play sessions is what sets Lego apart. This desire for excellence is a driving force in their ongoing success.
Conclusion: Choosing the Right Type of Injection Molding for Your Project
Injection molding is truly a versatile and reliable manufacturing method. Each step, right from material selection to mold design, to actual molding, plays a crucial role in creating the perfect part. With this understanding, you can confidently navigate the world of injection molding, secure in the knowledge that you’re making the right choices for your project.