Plastic Product Design Process: Key Steps Analysis
Introduction
Designing plastic products isn’t just about formulating a concept—it’s a meticulous process that requires a deep understanding of the purpose, the users, and techniques like injection molding to create a user-oriented product. Optimizing a plastic product design involves breaking down the process into key steps, including molding techniques, and understanding what each step contributes towards the final product.
Understanding Design
Every product starts with an idea. This is the core principle of any design. It’s critical to understand the users’ needs, design techniques such as molding, and design a product that not only fulfills these needs but also enhances the users’ experience. While aesthetic appeal matters, functionality, convenience, and understanding the role of injection molding and mold-making in creating a user-friendly and practical product are equally crucial.
Material Selection: Injection Molding and Beyond
Choosing the right material is paramount in the product design process. The choice of plastic would depend on various factors including the product functionality, aesthetic requirements, production costs, and most importantly – the injection molding process. Factors like material behavior during the injection molding process, resistance to temperatures and impacts, and aesthetics are key determinants of the right plastic material.
Initial Designing: Digging into Mold Making
Initial designing involves sketching out the idea, considering injection molding specifications, and creating CAD models for the product. It’s here the mold-making comes into play, where the product starts taking shape, keeping in mind the goals set out in the design philosophy and aligning the design with the specific injection molding process.

Prototyping, Testing, and Molds
Before full-scale manufacturing, creating prototypes and conducting rigorous testing is essential. This crucial step involves creating a precise mold to ensure the plastic part aligns perfectly with the design, followed by methodical testing to identify design flaws. Prototypes are often made by using the exact mold that will be used in the final manufacturing to get a realistic idea of the final product.
Manufacturing, Injection Molding, and Quality Control
During the manufacturing stage, effective quality control mechanisms are vital. Regular inspections and adhering to industry standards can ensure that the plastic injection molding process is successful and the final product is consistent with the design, being useful and practical, aligning with the initial design philosophy.
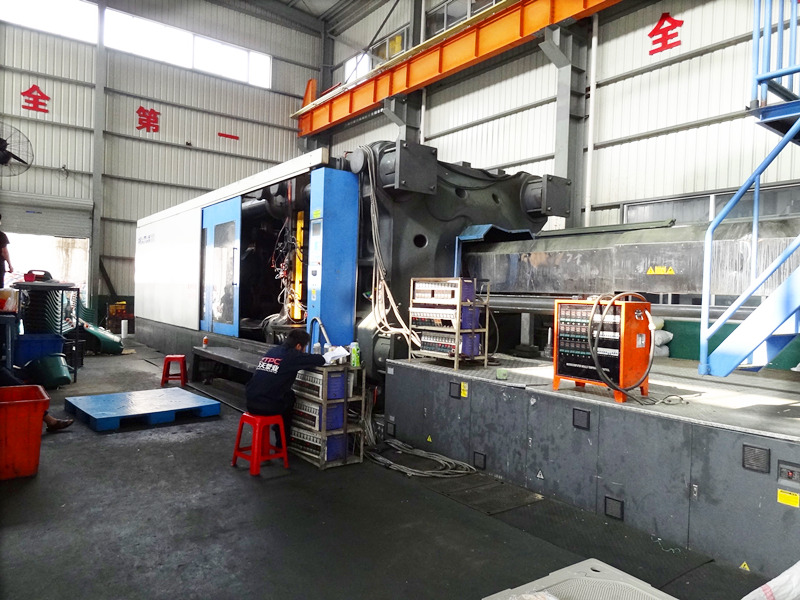
Conclusion
Designing a plastic product requires careful analysis of each key step in the design process, especially paying heed to injection molding and mold manufacturing techniques. By having a thorough approach, taking into consideration each minute detail, we can create plastic products that are efficient, user-oriented, and have a reduced impact on the environment. The realms of injection molding and mold-making are integral parts of the plastic design process that significantly contribute to the success of the finished product.