Precision Plastic Mold Manufacturing and Custom Automotive Fog Light Bezel Production
Client Overview:
Our client, a leading automotive accessories retailer, sought a reliable partner for the custom manufacturing of fog light bezels. Recognizing our expertise in plastic mold manufacturing and product processing, they provided samples, entrusting us with the task of replicating and enhancing the durability and aesthetic appeal of these bezels for their products.
Client’s Goals:
- Precise Product Replication: Achieve an exact match to the provided fog light bezel samples, ensuring a high level of accuracy and consistency.
- Material Innovation: Utilize advanced plastic mold manufacturing techniques to enhance the durability and aesthetic appeal of the replicated bezels.
- Comprehensive Manufacturing Services: Provide end-to-end manufacturing services, from mold creation to final product assembly.
Our Solution:
At Rayleap Plastic, we leveraged our extensive capabilities in plastic mold manufacturing and product processing to meet and exceed the client’s expectations:
Sample Reproduction:
- Received and analyzed the client’s provided fog light bezel samples.
- Utilized advanced mold scanning and 3D modeling technology to replicate the samples with precision, ensuring an exact match to the client’s specifications.
Advanced Plastic Mold Manufacturing:
- Employed state-of-the-art injection molding technology to bring the replicated bezel design to life.
- Implemented innovative mold cooling techniques to enhance production efficiency and maintain high-quality standards.
End-to-End Manufacturing Services:
- Provided comprehensive manufacturing services, from mold creation to final product assembly.
- Ensured rigorous quality control checks at every stage of the manufacturing process to guarantee the integrity of the finished fog light bezels.
Material Selection and Durability:
- Recommended high-performance and weather-resistant plastic materials, ensuring the replicated bezels’ longevity and resistance to environmental elements.
- Conducted material testing to validate the durability and performance of the chosen materials.
Results and Impact:
The collaboration resulted in a successful replication of the client’s provided fog light bezel samples, incorporating advanced mold manufacturing and precision product processing. Key outcomes include:
- Exact Sample Replication: The bezels precisely matched the client’s provided samples, meeting their design specifications.
- Robust and Durable: Our choice of high-quality plastic materials and precision manufacturing techniques resulted in bezels that met the client’s durability standards.
- End-to-End Excellence: The seamless integration of mold manufacturing and product processing showcased our ability to provide comprehensive solutions.
Client Testimonial:
“Choosing Rayleap Plastic for product our fog light bezel was a wise decision. Their expertise and attention to detail ensured an exact match to our specifications, saving us time and resources.”
Conclusion:
This case highlights Rayleap Plastic‘s expertise in plastic mold manufacturing and custom plastic molding, offering clients accurate replication, durability, and comprehensive services. For trusted collaboration and high-quality results in plastic injection molding manufacturing, choose Rayleap Plastic.
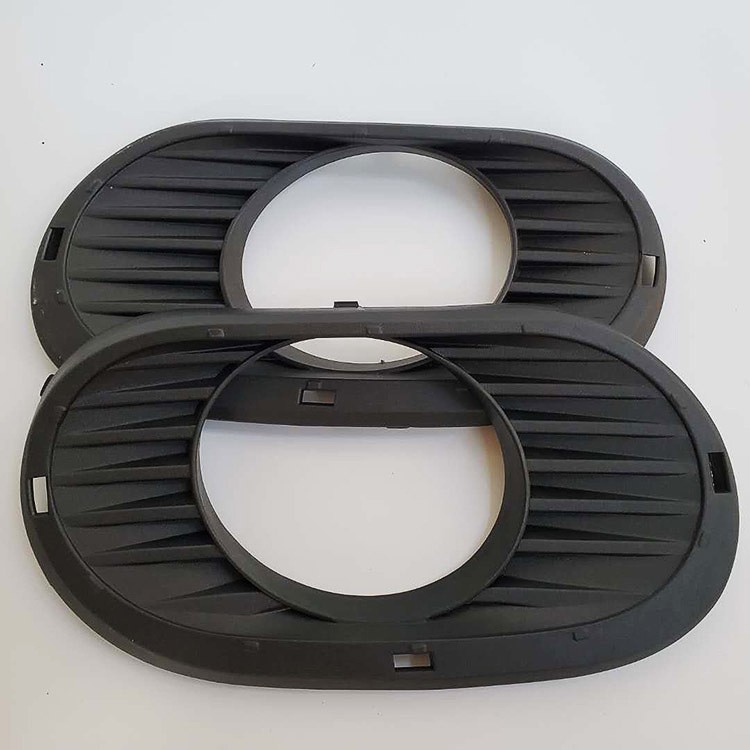
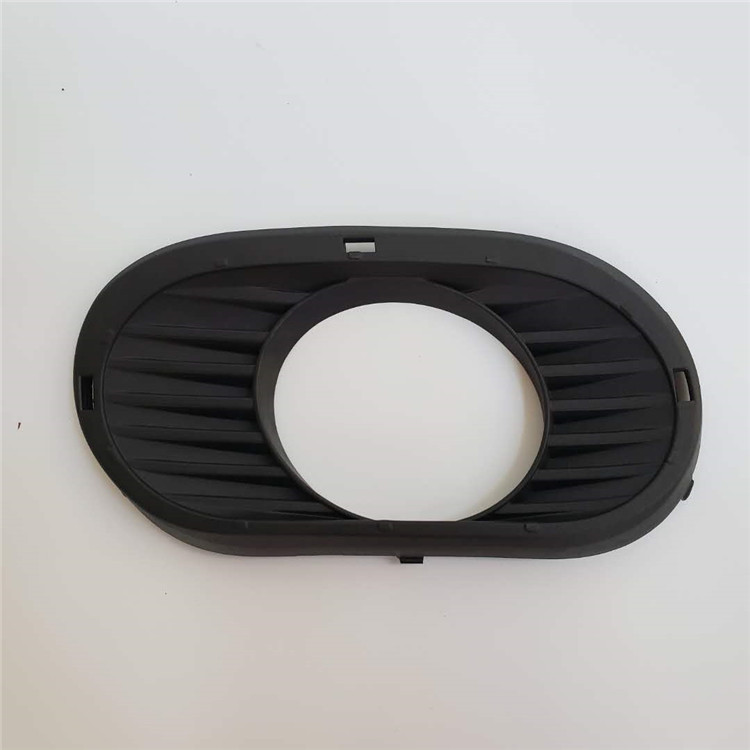